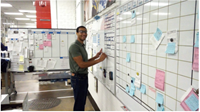
Welcome to #LifeWith3M, where our employees answer some of the most commonly asked questions we get from candidates like yourself, specifically about what it’s like to work at 3M. For this round, we’re highlighting the Optimized Operations (O2) experience with the help of two employees currently in the program—Jamal Sawyer and Alicen Johnson. Jamal is a graduate of the mechanical engineering program at Prairie View A&M University and is two months into the O2 program. Alicen got her master’s degree in Environmental Health and Safety at the University of Minnesota – Duluth and has been in the O2 program for nine months.
Here are the six most commonly asked questions about the O2 experience.
1. Is the O2 program for everyone?
Unlike some of 3M’s other programs that have a shorter timeframe, the O2 program is a two-year manufacturing and supply chain development program that provides recent Engineering, Supply Chain, Environmental, Health and Safety graduates the opportunity to jump-start their careers. Employees in the program work on challenging assignments and have rotational experiences geared toward inspiring them to be an improvement-driven, socially cognizant and globally aware professional.
2. Where do O2 employees work and do they get to choose their location?
The short answer is that you’ll work at a number of locations throughout the U.S. and won’t get to choose where. It’s scary, but ultimately rewarding, to accept a job not knowing the location. When Jamal and Alicen accepted positions in the O2 program, they didn’t know where they would be living for the next two years. “It’s definitely nerve-wracking, but I also realized that I’d be gaining great experience, meeting new people and seeing parts of the world that I never would have been exposed to otherwise,” says Alicen.
“It’s a mixture of fear and exhilaration,” adds Jamal. “We were told that we’d have to be okay with being placed in a small town or a big city and everything in between, so I was very anxious to get the phone call telling me where I’d be placed.”
3. Is there training involved or do participants jump right into the work?
There are five weeks of training but it’s all fun and very valuable. “During training, we received a broad overview of all the resources, programs and initiatives available at 3M,” Jamal explains. “For example, we did finance, Intellectual Property, disruptive technologies, insights, Lean, project management and Lean Six Sigma greenbelt training, just to name a few. Many of them were interactive or involved playing games.”
Alicen adds, “The training is valuable in helping you understand the tools provided to successfully complete your projects and advance your career.”
4. Does everyone in the O2 program work on similar projects?
The projects differ depending on the person and location. “The projects are focused around challenges the site is facing but is also dependent on your degree. You use the tools you learn in training and dive right into real life problems,” Alicen says. Jamal agrees, stating that he works on “reducing product to product changeover time, and redesigning or buying new equipment to reduce downtime on assembly lines, but other O2s work on projects increasing yield or decreasing waste on their assembly lines.”
5. Is it tough to transition quickly between assignments?
Integrating into a new location is tough, but the assignments are enjoyable. “It usually takes time for me to get settled and get the rhythm of things, but my current site is a fast-paced environment, so I had to adapt right away,” Alicen says. “But I love my assignment, and to be honest, I don’t want it to end, though I’m excited to see what’s next. I know that my least favorite part of this is saying goodbye.”
Jamal had a similar experience: “It was stressful and overwhelming at first because you are learning who people are and about your role, but I’ve definitely enjoyed my assignment so far and everyone has been so welcoming.”
6. Do the O2 participants get to work together?
While the projects are split up individually, O2 participants stay very connected to the other O2s. With 30 other O2's in Jamal's program wave and 11 in Alicen's, they got to know each other very well. “We get together every day for lunch and talk about our projects and our struggles. We also help and watch out for each other,” says Jamal. “We also all try to hang out together a few times a week outside of work.”
Alicen also has become very close with the other O2s in her group: “We talk almost every day! It is great to have people that can relate to the same things you are going through: projects, moving, meeting new people and doing new things. I know that these relationships I’m building will continue to grow throughout my career.”
Start your O2 experience.
To learn more about the O2 experience, fill out the Talent Community Form and select “Manufacturing” in the “Functional Area of Interest” section.
Multimedia Files: